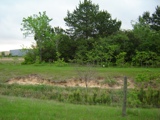 |
1.
When I took over the project the entire 54 acre tract was wooded
pasture. Cows ran the property and the landscape ranged from
swamped gullies to woods to open pasture. The carcass of a cow
led me into an area where the long dried bones of other dead
cows was scattered throughout the thick underbrush. This property
had long been used for agriculture purposes for running cattle
and I didn't want someone to later say that we had harmed the
cows so we added fencing and even stretched barbed wire ourselves
to separate the cows from the construction site. |
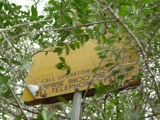 |
2. During my original review of the property
I found evidence of an old telephone line. The easement only
ran a few hundred feet and then terminated near the middle of
the property. Practicing "due diligence" and just for
good laugh I called the Operator and asked for "Enterprise
9800."
We did eventually get a release of the
easement made necessary because it continually showed up on the
plats causing problems with getting later easements that were
necessary for our electrical service.
|
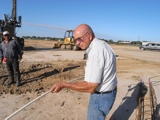 |
3. This is my trusty "side-kick".
This is the guy that makes sure that the people on site are doing
what they say they are. Be it at 3:00 am, on the weekend, or
until "dark-thirty", hiring Roy Weisinger was one of
the best moves we made. With over 50 years experience Roy proved
to be a major asset as contractors sought his advice and site
workers took his direction without complaint.
Here Roy has mounted a digital camera on
the end of a PVC pipe. He's set the timer on the camera to snap
after 10 seconds. Inserting the camera down into the boring holes
he took pictures of the conditions near the bottom where light
wouldn't shine so he could insure that the footer had been reamed
properly.
|
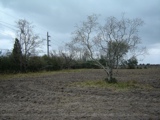 |
4. Proving that you have to keep an eye
on everybody. I had ordered all 54 acres completely cleared.
As the excavators and bulldozers were nearing the end of their
clearing stages this one tree stood out day after day. I asked
the operators why it was still there. Answer, "We didn't
want to clear it because it "spoke to us."
My answer was to ask, "When it spoke
to you, did it offer to sign the check for your services?"
Needless to say the tree was gone the next day.
|
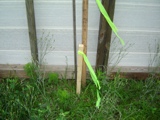 |
5.
The property had been surveyed a few years earlier but I considered
it my responsibility to know every inch of this project. Using
the survey map I walked to every marker. Once found I placed
my own marker and tape so that I would know and could be confident
in pointing out where the property lines were. This helped tremendously
as both County and State inspectors and officials came to the
site later in the project to determine our status of construction
and to fulfill their roles. |
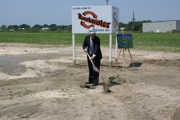 |
6.
With the land cleared we held a ground-breaking ceremony. Not
once, but twice. The first was for county dignitaries and longstanding
customers. The sign in the background was the one at the entrance
on FM 529 announcing the project. I moved it back to the groundbreaking
and then returned it once we had completed the ceremonies. |
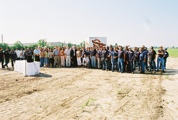 |
7.
The second was for the employees whom the owner attributes much
of his success. (Who wasn't in this picture? As a matter of fact,
who wasn't in almost every picture? Your truly. As usual I was
the one taking the pictures.) |
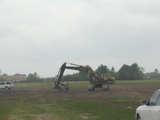 |
8.
Picking a location on the site where no buildings were slated
to be built a deep pit was dug. During the clearing process trees
and brush were piled for several weeks to dry out. Under authority
of a county permit the brush was burned in the pit under controlled
conditions. The fire pit, becuase of its proximity to the water
table, can not include anything but natural shrubs, trees, and
brush. No chemicals, no man-made matter, no cattle remains. Nothing
that seepage could take down the remaining few feet to contaminate
the water. With the property finally
clean the back-hoe operator covers the fire pit and packs it
down until there is no evidence it was every there. |
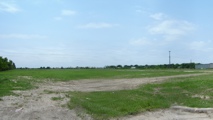 |
9.
Here the property is finally cleared and ready to begin construction.
During the process of clearing and making the ground ready there
were many meetings and details to attend. Working with the Civil
Engineers, Architects, banking officers, nearby property owners,
and MUD (Municipal Utility District) officers were just a few.
There are some environmental concerns I can not disclose on this
project. Nothing major but still affecting the schedule. |
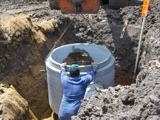 |
10. There were quite a few times that someone
at the old office would comment that nothing was going on at
the new site. A LOT was going on, they just couldn't see it.
After all permits and plans have been satisfied
with the county the laying of storm sewer is usually a hidden
process. I say "hidden" because folks passing by the
site on the highway don't see the workers. They are down in the
holes digging trenches and laying the lines and tanks.
|
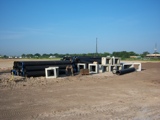 |
11.
As a fisherman I say, "Pollute it now..., eat it later."
This was just the first of half a dozen truckloads of underground
conduit and junction boxes that are typically buried under parking
lots or buildings. A site that was once capable of absorbing
rainwater now has to shed that water and do it so that it does
not create flooding conditions elsewhere around the property.
The amount of water has to be calculated and then diverted to
receiving areas of run off. Typically ditches or other forms
of drainage systems that are all part of the regional flood control
program. During and after installation the project is monitored
by county officials to insure that the plans are followed to
a T. |
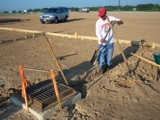 |
12.
Furthering that thought we don't typically consider that the
parking lot has to be designed so that run off is at a controlled
rate. Based on the amount of water, planning for a rain event
starts at where the water enters the highest drain. From there
the remaining components must be positioned so that the last
place the water leaves at the last drain is at or lower than
where it started from. Otherwise, water backs up into the drain
causing stagnation and foul smells to constantly waft from the
holes. |
 |
13.
Because this factory building and office is so large each column
requires a pier with footer. These holes and the concrete are
typically drilled down to "load bearing" surfaces.
Sometimes it is rock. Other times (as in our case) it is packed
clay down between 10 - 14 feet. |
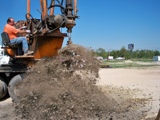 |
14. To make the process more efficient
three crews work together. Referring to the plans the drilling
crew first digs the hole using an auger. They then move to the
next hole while the bell crew reams the bell at the bottom of
the hole. Once that is done they move to the next hole location
and the concrete crew follows immediately behind. In this shot
the belling crew is barely clear before the concrete truck is
positioned to start pouring.
Another aspect of this level of new construction
as might be seen later is represented by this picture. Any time
you move dirt you have one of two options. (1) reuse it, or,
(2) relocate it.
|
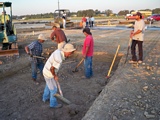 |
15. Having preplanned the location of heavy
factory machines the workers begin digging out squares where
thicker concrete will be poured. This is a monolithic slab where
the thicker concrete sections are poured at the same time as
the floor. The thicker concrete provides much needed support
for the heavy machines that would break the standard concrete
floor. It also allows anchor bolts to be drilled and firmly seated
so that the machines do not "walk" as might be caused
by machining vibrations.
These particular monolithic pours are much
shallower and very different from the machine foundations shown
later.
|
 |
16.
Once the monolithic slab holes are dug the rebar has to be specially
fitted to include the additional concrete. It appears obvious
that drilling into the concrete for the purpose of installing
anchor bolts would be hampered by all the steel. |
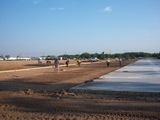 |
17. The general contractor decided to pour
segments lengthwise rather than across the shorter width. In
the beginning I didn't see where it made any difference so I
observed the process very closely thinking I was going to learn
something new. In the end, I still say it didn't make any difference.
So, in the terms of project management
this is one of those times when you simply don't make an issue
of it and let the GC work the way they want to.
|
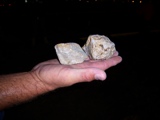 |
18. It's 3:30 in the morning. As I said
previously Roy Weisinger is on scene ahead of the concrete trucks.
They are ready their pour - but, within minutes Roy has a sample
of the concrete and immediately calls a halt.
These chunks of concrete rip-rap were in
the mix. This just proves why you need someone on site, at all
times and why you take samples of EVERY load. The samples with
their pour location were retained by the contractor (for a small
fee) to be held for a specific period of time. Should we have
failures of the concrecte we could pull the sample and see the
density and fill, etc., to determine if it varied from the contract
quality.
|
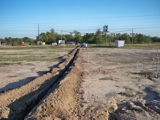 |
19. In addition to the concerns of underground
runs for your own site services you have to make certain to include
those services that come from outside resources such as the Electric
Company, the Telephone Company, the Gas Company, and Water/Sewer,
etc.
Point: As the project manager you have
to make certain that YOU are aware of every service run, that
you know where they are coming from and where they are going,
and how they plan to get there. You cannot leave it to chance
nor can you leave it to them to figure out and do as they please.
|
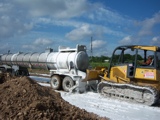 |
20.
Part of this project included the development of Thrustmaster
Drive. First slated to be a county road along private property
with an easement that would have provided a payback, the city
and county planners both eventually got involved. What started
as a simple road to allow access with large truck traffic turned
into a major county road. In addition there was another intersecting
road that went nowhere except to split the property into two
sections. Literally, it was only planned for the future and did
nothing for the next 20 years. The owner then decided to pay
for it himself and in exchange, had the road named according
to his desire. Thrustmaster Drive. |
 |
21.
Hurricane Rita heads for the Gulf Coast. Needless to say construction
is put on hold as workers from around the Houston area turn their
attention to taking care of family and homes. Our family covers
from Orange County to Harris County so regardless of where the
storm hits, we are all going to be affected. And we were. But,
thanks to the Lord that no one was hurt we all pulled through
and within a couple of weeks were back up and running full steam.
We knew in advance were we could aquire the generators we need
to keep the factory running. |
 |
22.
Thrustmaster decision makers pull in a MEGA-GENERATOR and connect
up to the main power. Manufacturing keeps running for days as
this monster pumped out the kW's. Those tanks in front are diesel
fuel which was consumed at about 250 gallons per day of operation. |
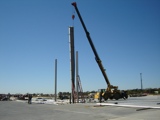 |
23.
Finally, the first steel is erected! As you can see in this photo
the first column on the north-east corner goes up without much
fanfare. If you look closely you can see that there is a lot
of concrete on the ground. |
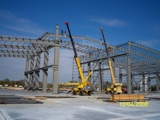 |
24.
With the foundation established the frame structure begins to
move very quickly as the frames and beams were all pre-fabricated
to fit. It is far from an erector set which has holes strategically
placed to allow for a variety of assemblies. In this case if
a set of holes are off my mere inches there is going to be trouble
down the road. Either the holes have to be fixed on site, or
the holes have to be fixed on site. In other words, when you
start assembling this kind of structure there isn't much choice. |
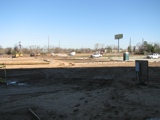 |
25.
Out front the factory office building continues at a much slower
pace. In part because the same workers and equipment needed for
the office are working on the factory. Part two, because the
office building is far more complex in the amount of "layers"
it will take to build it. |
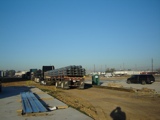 |
26.
Finally! The steel for the office building arrives. In this photo
I pulled one of my no-no's and accidentally got my shadow in
the picture. The four truckloads were the first round of three
more deliveries that would come over the next two weeks. This
photo was taken on Jan 15, 2009. |
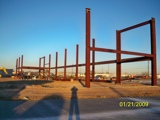 |
27.
Second no-no. Did it again! Or did I? One "tell" is
the date. This photo was taken by Roy. This photo can also indicate
the approximate time. If you know that (1) Roy is facing west
north west, (2) the sun is rising directly behind him, and (3)
the long cast of his shadow you can tell that the sun is just
coming over the horizon so it's very early in the morning. This
is the condition of the site on Jan 21, 2009. |
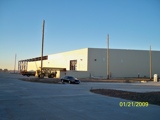 |
28.
On Jan 21, 2009 you can also see progress of the factory. More
importantly for us, after the hurricane our electrical service
was put on the back burner by Centerpoint as their crews were
tied up repairing downed and damaged power lines around Harris
and Ft. Bend counties. This photo shows that by mid January we
have the poles and hardware in place, however, the service is
still not ready. Throughout this time the general contractor
is working with one single electrical service point between the
buildings. The extension cords are getting too long so generators
are deployed to supplement the lack of electrical services. |
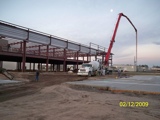 |
29.
A concrete pump truck moves into position. In the background
you can see that the building is coming together. This is on
February 12, 2009 and the second floor is getting ready to be
poured. One thing about this project is that the General Contractor
kept things moving. When we couldn't work on the building, or
he had an excess of manpower he put them to pouring or getting
the site ready for parking lot pours. |
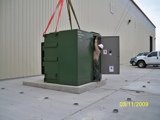 |
30.
Finally, Centerpoint arrives with the the main factory transformer.
These transformers have to be ordered 6-9 months in advance so
when you start such a project you want to determine your anticipated
power usage and get the electrical provider on the line early
and get this one item ordered as early as possible. Another early
stage item is to understand the requirements for the pad, and
for the barriers. Here you can see that we've already set inserts
for the barriers so that we could pour the parking lot. The pipe
barriers would be inserted into the sleeves and cemented in later. |
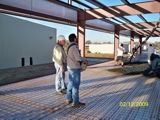 |
31.
Yours truly standing with the pump truck operator as we pour
black concrete on the second floor. Although warned that the
concrete would crack, and were even taken to another facility
and shown the results, it was decided to go ahead and pour anyway.
The concrete did just as promised and the cracks were just too
much so the second floor was finished with carpet and tile. It
turned out beautiful. |
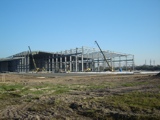 |
32.
The factory is progressing quick although we would like to have
made it much faster. We were working against a production deadline
as well as a construction loan deadline and regardless of the
affects of the hurricane, we needed to be in and cutting steel
within the next 4 months. |
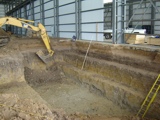 |
33.
Timed with completing the roof the first phase of building a
foundation for a CNC Machining Center is built. The leave-out
and resulting excavation for this project was larger than my
first home. |
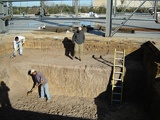 |
34.
Workers in this scene give a better perspective of the depth
of this tiered hole. The worker standing at the bottom represents
where a solid concrete monolith will be poured. This will serve
as the foundation for the new CNC machine. |
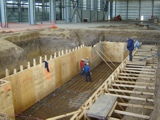 |
35.
The form is being set for the first pour. That block will be
isolated by a 3/4" fiber shell and the next layer poured.
Then a third until the foundation is completed by the "apron". |
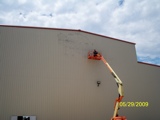 |
36.
A contract sign painter outlines the unique Thrustmaster logo.
Not such an easy task on a corrugated wall. I had just completed
converting the raster image into a vector file in AutoCAD and
Illustrator. The sign painter used that file to layout his pattern
for painting the logo onto the building. |
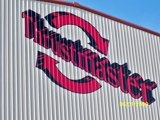 |
37.
The Thrustmaster logo is finished. We thought about painting
that logo onto the roof so the next time a satellite passes to
take a photo and replace those on Google (TM) and such sites
the building could be seen from space. As it is you can Google(TM)
the address and see it clearly. Furthermore, we were teasing
the idea of putting photovoltaic cells on the roof so the sign
would have been a waste. |
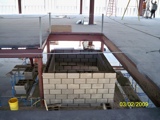 |
38.
Obviously, in building construction the project is the entire
building, not just one floor. There is no such thing as any single
floor affecting only itself. Likewise, the elevator shaft, AC
ducting, chases for wiring and plumbing, and stairwells are examples
of the kinds of "multiple floor high impact" issues
construction projects face. Our design on this elevator shaft
is to also include the circular stairwell between floors. This
minimizes the amount of space needing to be dedicated to both
since they share the same opening and footprint. (The stairwell
was eventually squared but still went around the elevator shaft.) |
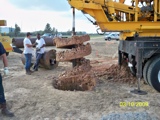 |
39.
Barely down 8 feet and we are seeing water in the clay. Our boring
surveys showed something else that made the steel pipe in the
background necessary for setting the piers. Throughout the area
there were layers of sand and silt that would collapse or sluff
off before we could pour the concrete. In this case the sleeve
would be inserted into the hole before the walls sluffed off.
This allowed re-bar to be inserted without worrying about hitting
the walls. Concrete would then be pumped into the sleeve as it
was withdrawn from the hole allowing that the pressure of the
concrete would push against the looser sand and silt while it
set and prevent the walls from collapsing. |
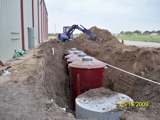 |
40.
The septic system is being installed. One of the delays encountered
during early planning was that the MUD district was having an
issue with another property owner about getting our sewer and
water lines connected. It was also discovered that the water
line was not capable of delivering the amount of water demanded
by our fire suppression system. Rather than wait any longer we
permitted and installed our own septic, water wells, and fire
pump and hydrants. |
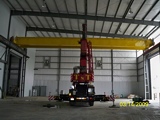 |
41.
Installing one of the 7 new cranes. The largest is a 100T with
a 30T auxilliary used for turning large thrusters. |
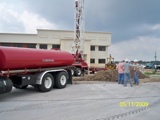 |
42.
At first the drilling of the well directly in front of the main
building was considered a crazy idea. The challenge was that
we had to be a certain distance back from FM529 and a certain
distance from our second well. While these are considered private
wells they meet the criteria of a public water source and as
such must be inspected every day with reports going to the city
and county. (A recent test in a Louisiana public water system
showed evidence of an omeba which could cause brain swelling.
Thankfully Thrustmasters water is safe and good to drink from
a 300ft deep aquifer.) The well was surrounded by a picket fence
that matched the landscape using palm trees and a flower bed
that "wanders" along side the main walkway. |
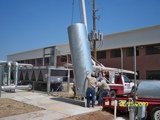 |
43.
The pressure tanks also serve as the location for the chlorine
house and chlorine induction system. To the left of the tank
is one part of the 500T chilled water system that will cool the
factory and office alike. In the event of one half of the system
going down the other half can still cool the office and keep
the factory at a reasonable level to allow the temperature sensitive
machines running. |
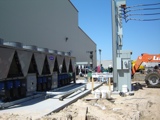 |
44.
While it may seem such a small concern something as simple as
a sign indicated the address for electrical services installation
can actually delay a project for days or even weeks. If you are
scheduled to have the service connected, and the sign is not
present, they will not install and that moves you to the bottom
of their list. It can be weeks before they get back to you so
put anything like this, no matter how insignificant it seems,
on your MS Project Planning and make sure it gets done. |
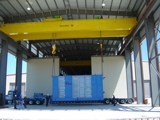 |
45. The 100/30 ton crane travels out the
back to load and unload large thrusters onto trucks. The door
opens to the shape of a T allowing the crane to pass through
without fully exposing the air conditioned factory to the full
onslaught of Texas heat and humidity.
This area out back has been converted to
a test area.
|
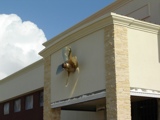 |
46.
The entrance to the building boasts a 5000lb NiBrAl prop that
was polished and mounted to a shaft sitting atop two bearings.
The entrance had to be reengineered to hold the additional weight
in a 110mph wind for 2 hours. We estimated that turning only
2 rpm, with the bearings being maintened properly, should have
a life of about 3000 years. |
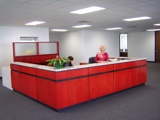 |
47.
The reception desk was designed between myself, the recepionist
Pat Little, and the owners wife, Corry Bekker. I modeled the
reception desk in AutoCAD and took it to Impressions Millwork in Cypress, TX. Brian
Dumaine, Chief Designer & CEO, took our concept and ran with
it makeing this beautiful piece of funcitonal art. |
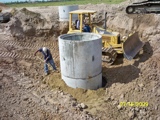 |
48.
This concrete well is being set in order to install the suicide
fire pumps to the pond below. There are two pumps feeding a pressure
tank which maintains pressure on the factory and office sprinkler
system. When the pressure drops in the tank the first pump automatically
starts and stabilizes the pressure. If the first pump can not
maintain the pressure, or fails to start over a period of time
the second put starts. |
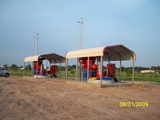 |
49.
These are called suicide pumps because there is no safety involved.
These pumps run until they die or the fire is out. They are inspected
on a regular basis and the fuel is replaced as needed to keep
the pumps ready for a fire. They have since been enclosed with
a fence to keep the cows out and for additional security. |
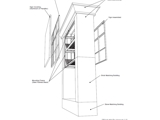 |
50.
Signage for the front entrance is developed using AutoCAD to
define the general layout and plan for accessing the sign and
lighting inside. The 3D model (right) gives an idea of how it
would have appeared with the building in the background. |
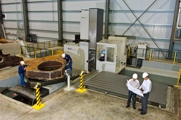 |
51.
The Giddings - Lewis CNC prepares to run its first part. The
two employees stretching the tape were not doing so for any reason
needed by the CNC. They were setting up a fixture in QC to mount
the thruster base for checking once the part was completed. |
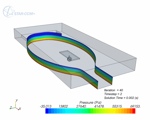 |
52.
The test pond, planned to be 35 feet deep, was analyzed with
the companies hydaulic software. In the center is a model of
a thruster. The colored zones show how the pressures would have
progressed throughout various thruster speeds over time. Before
completion we determined that we would also need to build a 15ft
wall along the back of the test pond to prevent the water from
spilling out and requiring refilling with each test. |